行业新闻
热点访谈:一体化压铸成型、压铸机超大型化趋势,推动压铸技术革新与行业发展
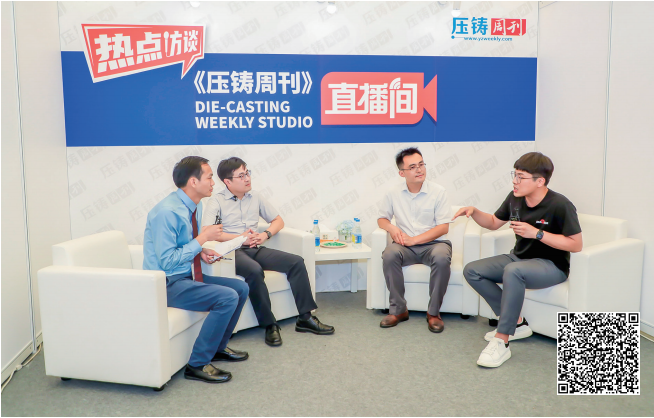
上汽通用汽车有限公司技术经理朱昱(左二),博世(中国)投资有限公司高级铸造专家丁翊伟(右二)以及迈格码(苏州)软件科技有限公司高级应用经理刘琪明(右一)做客热点访谈“直播间”。
“第十六届上海国际压铸展暨2021上海国际有色铸造展”已于2021年7月7-9日在上海新国际博览中心成功举办。展会期间,主办方中国机械工程学会铸造分会(下称 “铸造学会”)、《压铸周刊》联合推出“对话行业专家:热点访谈”节目,邀请两组圆桌论坛专家走进“直播间”,就“新能源车零部件一体化成型、压铸机超大型化的趋势,推动压铸技术及应用革新”和“低压/重力/挤压铸造、半固态成型、高真空压铸等铝铸造新工艺变革与推广应用”两个话题展开探讨,本期针对第一个话题节选刊登。
1 嘉宾简介
朱昱:上汽通用汽车有限公司,技术经理
丁翊伟:博世(中国)投资有限公司,高级铸造专家
刘琪明:迈格码(苏州)软件科技有限公司,高级应用经理
2 对话内容
《压铸周刊》:2021年度压铸行业创新技术与产品评选”中,十项创新中三项是超大型压铸机,一体化成型、压铸机超大型化趋势之下,铸造行业发展受到怎样的影响?压铸企业如何快速进入新领域?
朱昱:“减少装配的数量,简化装配的工艺方式”,这两条在装配制造领域早已提出过,特斯拉引领大家充分运用这个概念,并在压铸行业取得了突破性的进展。这个突破性的进展不仅仅是压铸机的大小,还有压铸模具的大小,随之而来的工艺技术升级,以及一些检测设备,这些都是处于超大型设备和一体化成型的趋势当中。受其影响,国内的新能源车企,一些合资品牌和个别合资厂的自主品牌,形成了一个将参与第二波大型一体化压铸成型趋势的团体。这个团体的形成进一步增强了整个行业对这个方向发展的信心,进一步推动了压铸件大型一体化成型的进程,更加大了投资力度。通讯5G市场的发展,零部件厂也需要扩能。势必要大型化来适应物流的周转,各方面的升级都是为了潜在的大型化压铸件市场。国内许多模具厂出现扩厂,以适配大型模具制造,零部件生产厂扩能,从设备、模具到工艺设计,需要不断的技术升级,并始终坚持产品的可制造性。
丁翊伟:博世发展中有一个理念是合作共赢,博世和供应商是合作伙伴,合作伙伴采用大量的压铸结构件,铝合金、镁合金压铸件以及铸铁件等,合作交流是双向的,同时也会对合作伙伴进行支持。针对大型化、一体化成型的趋势,企业自身要做到三方面提升:第一,压铸企业要同以往一样注重精益性,推行精益生产模式,从产品设计开始,包括对产品的工艺制造设计,产品的结构分析等,确保产品的工艺性是适用的、可制造的;第二,希望压铸企业把数字管理的理念导入到企业管理中去,实现数字化、精细化、可视化经营,把可变动的因素导入到数字的因素来管控它,这样压铸的指标会更加量化;第三,希望压铸同仁和企业拓宽全球视野,更大的格局会让合作走得更远。
刘琪明:针对大型一体压铸结构件,结合我之前做过的报告,对其认识重点在于温度、真空、成型方案、工艺参数、后处理、原材料几个方面。模具的温度主要通过两方面控制,一方面模具表面喷涂,另一方面模具内部通过冷却系统,目前真空方面可以达到超级真空30mbar,这一方面可以满足我们的质量要求。结构件成型时需要保证流态稳定,减少卷气等等。配备后处理可以直观看到质量,一些微观组织,以及力学性能如屈服强度、抗拉强度延伸率,软件可以呈现出成本的降低以及效率提高。压铸企业在提升自身的能力之余,可以结合模拟等方式进行研发与生产。
《压铸周刊》:在2019年上半年时,国内最大的压铸机是4500吨左右,随后2019年底力劲推出6000吨设备,至今年四月份力劲又推出9000吨巨型压铸机,超大型化趋势形成迅速,颠覆整个压铸行业原来的生态,基于这样背景下,大型一体化成型发展将给整车厂、产品开发以及模拟等领域带来哪些机遇和挑战?
朱昱:从整车角度来看,一体化成型带来的挑战主要有以下两方面:一方面,行业发展初期,一体化成型如何做到兼具功能性与工艺性;第二,国内车厂情况不尽相同,某些车厂处于扩能阶段,某些车厂处于产能富余阶段,还有一些整车厂自身可以压铸生产,它具有一定的人员和技术的储备。对于这类企业而言,更容易走向一体化这样的道路。而有一部分企业,需要外购铸件和锻件,在压铸方面,不具备研发团队或者系统的储备,这类企业很难从传统的已经掌握非常成熟的技术上面脱离开来,因而他们走向一体化这样的道路具有一定难度的。对于不同的车企面对的情况不一样。同时带来的机遇也是很明显的,轻量化增加产品的竞争力,降低制造成本。同时,作为第一波、第二波进入或者引领潮流的车企在一体化的道路上,从两方面提升其品牌的影响力,一方面是消费市场上,其它企业会认为这样的品牌是高科技的品牌,增加了企业的形象。另一方面是在资本市场上,同样会引起企业的关注,对于崛起的新能源汽车是非常关键的。
丁翊伟:站在我的角度,新能源引起的大型结构件开发,具有很多优势,减少工件数量和工序,降低制造成本,压铸成型精度较高,压铸件重量较轻,降低整车的能耗。一体化成型是大趋势。在此之上,建议企业可以结合三个方面更好的应对这一趋势:第一,继续进行精细管理,从产品设计开发,包括产品结构性、工艺优化、结构优化、模流分析,早期预判产品的缺陷,在早期消灭缺陷,加强精益性;第二,要有信息化管理,要做数字化生产的转型;第三,提高从业人员素质。压铸行业当前的发展非常迅速,需要企业追上来,这样会得到更好的发展。
刘琪明:以我们公司为例,一体化成型带来新的销售机遇,此同时也带来一些挑战。针对结构件,它需要的壁厚很均匀、很薄,模拟计算的时候增加计算的量,大型结构件尺寸增大,更加增加计算的量。除此以外,目前情况,模具厂传达给设计部的开发周期仅有一周,包括模拟出方案、开模,模拟的时间仅剩余半天至一天,时间明显不足,这两方面对于所有模拟公司均是挑战。
《压铸周刊》:一体化压铸成型大规模的应用推广还有多长的路要走?企业发展需要在哪些方面加强?如何突破瓶颈?
朱昱:具体需要多久无法给出定论。结合硬件和软件具备的条件来看,压铸机厂家的产能非常紧张,最好的超大型模具厂今年交付约10副大型模具,对于实际厂家的需求来讲远远不够。另外,根据模具厂的生产结构,大概今年最早一批投入的新的厂房到明年年底能够开始投产,增加的数量仍然有限,并且对硬件要求越来越高,早期希望的是4500吨发展至今为9000吨,对压铸设备要求越来越大。为了突破这一瓶颈,可以从两方面着手,第一,设备改造升级,不断革新,设计出并利用好大型设备;第二,提高压铸相关从业者身的技术水平,加大对大型化发展的了解以及加紧大型化设备设计的学习,不断更新自身的知识。
刘琪明:目前形势从技术角度来看,完成从无到有的突破,“没有压铸,到出现压铸,再到多方向压铸”,完成了从0到1的过程,并且在接近于1的路上,已经有成功的车厂特斯拉并且已经具备一定的产量,剩下需要做的是突破式的增长。目前已经建立很好的团队协作意识,例如已经存在案例,车厂将一级供应商、零件厂、模具厂以及辅助配套的材料、真空、模拟、热处理各个方向的专家汇聚到一起,一起集思,献言献策。材料方向的厂家尽最大努力,设计热处理材料,解决成型过程中气泡问题,真空方向最大限度让气体方面的问题得到一个解决,压铸机厂呈现其规划,车厂提出自身的需求,各个方向专家介绍其的能力,彼此合作,未来发展更需要加紧团结协作来面对不同角度的问题,来满足不同层面的需求。
《压铸周刊》:如何看待一体化压铸的成本优势和技术成熟度?
丁翊伟:关于成本优势,据行业统计经验,与传统冲压焊接成型相比,一体化压铸减少零部件数量和工序,减少生产设备减少人员消耗,综合来看,大概节省20~30%左右成本。关于技术成熟度问题,大型压铸在内的任何一种新型技术,均有婴儿期到青少年期的过程,但行业中特斯拉实现了一体压铸,我们已经出现这样的技术,虽然没有具体量化技术成熟度如何,但是它会指引行业中从业者向前行进。而我们行业其他从业者所需做的是加大这方面的力度,努力发展得更好,将一体化压铸普及。
朱昱:关于成本问题,其中一部分是质量成本,制造中热加工的零件从开发、投产到稳定量产,工程师需要花费很大的精力进行管理,即料废降低和产量爬坡的过程。而对于这类大型化结构件在投产的时候做到多少的废品率?需要花费多久能达到稳定的状态?这是我们作为质量工作者比较关注的,而这一方面仍有待于提高;另外一个是碳中和层面,国家最高领导人习近平主席在联合国大会上全世界做出的承诺,二氧化碳排放力争于2030年前达到峰值,努力争取2060年前实现碳中和。许多的机构已在评估政策,怎么制定政策能够满足2030年的碳达峰。同时政策要提前公布政策,给予企业响应的时间,这个我们目前一个阶段需要面对和解决的问题。整体来看,压铸成型一体化缩短制造工序,降低能耗及制造成本,同时也契合国家的发展方向,是对我们国家大政策层面的加持,是对全人类发展有益的。
Tags: 一体化,大型化,压铸